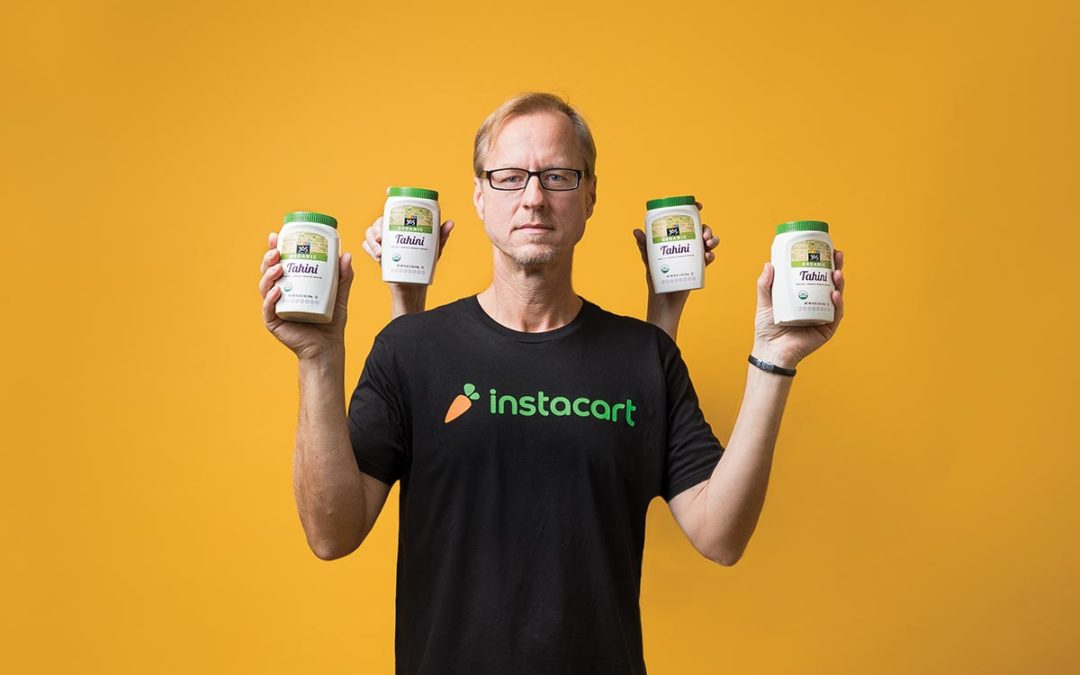
Food Movers: Confessions of an Instacart Shopper
He’s standing near the fresh herbs, staring at a forest of tiny green bundles, scratching his head, looking up and down from his phone. I offer some help, and he asks, “Where’s the basil?” After I help him choose a perky bunch, he thanks me and mumbles, “I hate shopping for vegetarians.” He’s wearing a shirt emblazoned with the Instacart logo.
Twenty minutes later I’m back in the produce section, and the man is still staring at herbs, looking defeated. “She wants fresh sage, not dried sage. What is it with these vegetarians?” he grumbles. In his defense, none of the herbs are labeled. I point out the fresh sage and wish him luck.
Those increasingly ubiquitous personal grocery shoppers roaming the aisles at a supermarket near you are paid a per-order bonus in addition to the minimum wage they earn per hour. The more orders they can complete in an hour, the more money they can make. But when they can’t find the right fresh herbs, like the shopper I encountered, their slowed quest results in fewer completed orders that day: in other words, money left on the table.
“If you do enough orders in a day and you’re really fast, you can make a lot of money,” explains a different Instacart shopper nearby.
Personal food shopping services have grown by leaps and bounds in the last few years. In Austin alone, six companies offer a range of personal shopping and delivery services at more than 10 stores. Nielsen’s Food Marketing Institute predicts that by 2025, 70 percent of consumers will be purchasing consumer packaged goods online. According to One Click Retail, Amazon already holds 18 percent of all online grocery sales.
That said, grocery shopping can be deeply personal. Customers have habits, preferences and quirks that retailers must accommodate with their third-party hand-picking-produce abilities.
“Ask anyone at HEB if they’ve had to find tahini and they’ll tell you, yes, it’s the hardest thing to find, and everyone wants it.”
As one shopper explains, “The people at Whole Foods are, well, ‘Whole Foodsie,’ ordering $50 jars of honey” and giving picky instructions about their produce. Because of this fastidiousness, online grocers started out offering only consumer packaged goods — pantry items like rice, beverages and breakfast cereals. But lately, most businesses have developed strategies for also offering fresh produce.
Still, online grocery shopping has room to grow. Less than 10 percent of customers in North America buy their fresh groceries online, according to Nielsen. Companies like Instacart have developed technologies that enable customers and shoppers to communicate as the shopper moves through the store. It’s a handy way to reassure customers that they’re getting exactly what they want. But shoppers may find their flow disrupted by picky comments such as, “Can you make sure to get the salmon that’s fourth from the back with the horizontal grill marks?” Or more frustrating: “I’m allergic to that brand.” Customer demands can get extreme, and shoppers feel the need to be polite even as they try to round up everything on their list.
Each company operates slightly differently for shoppers, who tend to stick to one company and one unique store. One exception is Burpy, which operates like the Uber of grocery delivery. Burpy shoppers may fulfill one order with products from a variety of stores. Shoppers are also paid differently depending on the company, ranging from minimum wage with bonuses per order, to flat hourly rates, to tips only. Shoppers generally work flexible schedules, which makes it an attractive second job or a good fit for students.
Regardless of payment criteria, speed matters. Shoppers create efficient strategies for moving through stores. Texas regional grocer HEB even has a digital platform that sorts a customer’s order according to the store’s unique layout, creating a “perfect workflow.” But despite deep store experience and superior technology, some items are still elusive to shoppers.
“Tahini,” one shopper says. “I’ve worked at five HEBs, and every time it’s a wild goose chase. I think it likes to hide itself. Ask anyone at HEB if they’ve had to find tahini and they’ll tell you, yes, it’s the hardest thing to find, and everyone wants it.”
Even when shoppers find everything on the list, customers must still get the groceries home. Because customers see only an itemized list, they often don’t realize how large their order is — an especially risky scenario when it’s for a pickup service or orders from Costco. Sizable orders of bottled beverages pose serious challenges.
“They pull up, and we’re dragging out three carts of groceries, two of which are full of bottled water, and they pull up in a VW Bug,” complains an HEB Curbside shopper. Amazon Fresh shoppers experience the same problem: “People will order 40 boxes of La Croix seltzer, and it’s crazy! You need eight shopping carts and that’s a lot of work.”
Despite the interconnected relationship between shopper and customer, an interesting disconnect remains. Shoppers frequently work in stores in which they do not personally shop, and often shoppers are asked to select items out of their comfort zone, like fresh herbs or fine wine. It begs the question: Can personal shoppers overcome these barriers to make this platform the future bread and butter of grocery shopping?