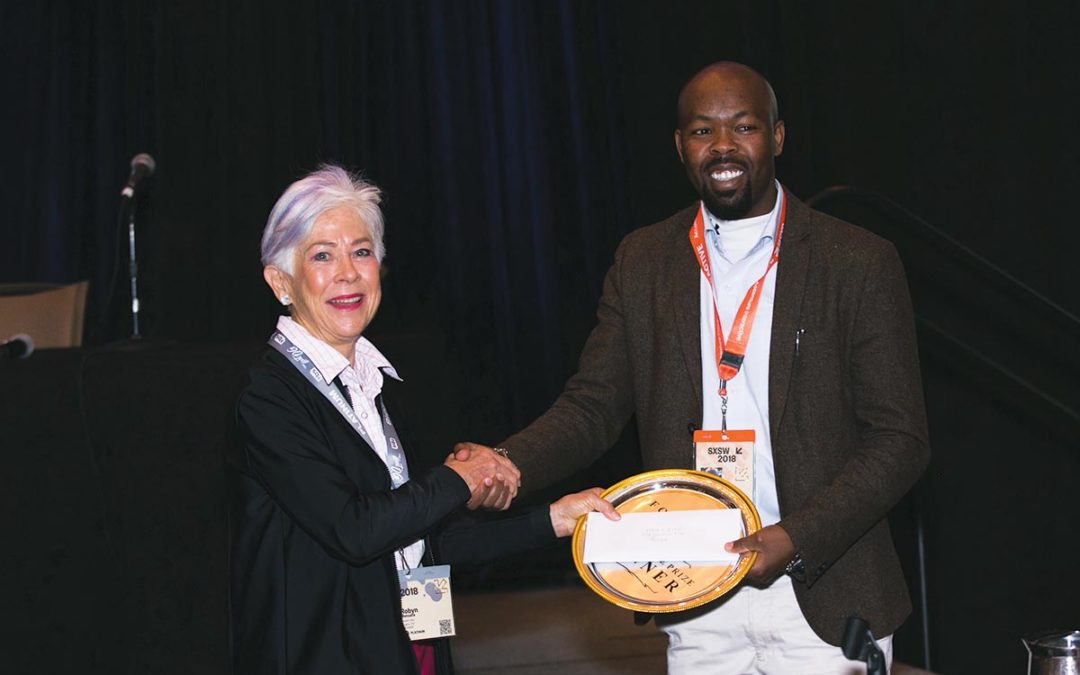
Where Are Food+City Startups Headed?
If the 2018 Food+City Challenge Prize entrants are any indication, we’re well on the way toward improving our food system.
Four years into our competition for food supply chain startups (read about all four years’ of finalists), we’ve noticed some interesting trends, including changes in the way entrepreneurs think about innovation. Progress is apparent despite food regulations, a lack of consistent data standards and the companies’ need to achieve scale while remaining small and agile. For many startups, technology is central — but it’s not necessarily all about apps anymore.
Instead, futuristic tools that bring new rigor to agriculture and warehouse management are on the horizon. UAV-IQ Precision Agriculture, one of three $10,000 Food+City Prize winners, provides precision crop monitoring for farmers using drones and sensors. The new technology enables farmers to use the gathered data to make decisions about resources to maximize their yields and reduce crop losses.
“UAV-IQ is attacking the fundamental lack of precise knowledge of where variability exists within fields,” says co-founder Andreas Neuman, former assistant director of operations for the U.S. Air Force’s Global Hawk Unmanned Aerial System. “This lack of knowledge and suitable toolkits to first identify and then manage variability leads to massive inefficiencies due to one-size-fits-all approaches, which often result in over-usage of water and chemicals.”
Another high-tech agriculture solution is Transaera, which is commercializing a material developed at the Massachusetts Institute of Technology that absorbs moisture within greenhouses. The product gives indoor farmers more control over their growing environments and enables them to reduce plant disease and increase yield while also reducing energy consumption.
“To feed nine billion people by 2050, we need new agricultural systems,” says founder Sorin Grama. “Indoor agriculture could be an answer, but it is an energy-intensive operation that will not scale unless we figure out how to grow foods using less energy and water.”
Entrepreneurs are also using technology to connect links in the food supply chain. For example, Stowga, a London-based business-to-business startup, connects retailers to unused warehouse space. This “Uber for warehouses” helps firms with excess storage use their space more efficiently; and it offers below-market options to businesses that may need space for only a short time.
Team mentor PJ Tanzillo, head of product at Favor Delivery, has high expectations for Stowga, led by CEO Charlie Pool. “Charlie and team are not your typical early-stage startup,” Tanzillo says. “They have a clear line of sight to a sustainable business, and they have achieved product and market fit. I’m confident their success will continue.”
Making connections across chain links continues to be a key draw for startups. Vinder is a digital platform that connects home gardeners who grew more than they can eat with community members who seek freshly grown food. Sam Lillie launched Vinder by going door to door in his hometown of Port Townsend, Washington, asking residents whether they had home gardens and if they ever had extra produce they’d be willing to sell. It wasn’t long before Lillie connected dozens of home gardeners with produce-hungry families, moving more than 300 pounds of fruits and vegetables among them.
“We have been trained over the last 70 years to buy our produce and processed goods from a giant supermarket chain that sources products from all over the world,” says Lillie. “Vinder reduces the food waste that happens in every city across the country while efficiently reducing delivery miles because you are buying from your neighbor and not some farmer in Argentina.” With the Vinder website and app, consumers in dozens of cities in 11 states can connect with nearby growers to buy the produce they seek, reducing food waste and putting money back into their communities, literally at the grassroots level.
If you don’t have a garden but want to grow your own food, Indiana-based Aggressively Organic, one of three Prize winners, can help. It offers micro-gardening systems for people without access to earth-based gardens. Users can grow lettuces, tomatoes and other fresh veggies in just one square foot of space in their homes. Anchored by cardboard “micro-growth chambers,” the hydroponic systems use a mere 16 ounces of water to grow a head of lettuce. In contrast, conventionally grown lettuces require 25 gallons of water per head.
“Instead of cut-and-kill or pull-and-ship — like all other current modalities of agriculture that end up shipping already dead and dying goods that end up being wasted — our stuff stays living, and we harvest when hungry,” says founder Jonathan Partlow.
Vinder and Aggressively Organic aren’t the only companies working on solutions to curb the growing amount of food waste. The 2018 submissions included ideas for moving excess food to consumers and methods for repurposing waste such as spent grains from beer breweries as ways to limit the amount of waste that ends up in the landfill.
The most tenacious and complicated problems that startups try to solve involve aggregating and transporting food from local producers to markets, restaurants and grocery stores. It’s a problem that food hubs have tried to solve for years. Today’s startup teams are working on a range of platforms: from apps that aggregate farm inventories to hauling and logistics businesses that focus on the transport of food from local producers to consumers. One of our contestants, GrubTubs, retrieves food waste from restaurants, turns it into compost for local chicken farms and then provides eggs back to the restaurants.
Another, Houston-based Grit Grocery, brings the grocery store right to your neighborhood, using a food truck model. Consumers no longer have to travel to the fringes of their communities to shop at energy-gobbling big-box grocery stores. Instead, Grit Grocery trucks bring locally grown produce, local honey and meal kits — featuring, for example, shrimp from the Gulf of Mexico — right into communities, shortening the last food mile and cutting the distance from farm to table.
“The shopping experience fundamentally shapes the flow of food, not only by creating limitations on what kind of food can be supplied but also by subtly creating demand for certain foods or even entire categories of food,” says Dustin Windham, who founded and operates Grit Grocery with partners Michael Powell and Jamal Ansari. “Building on that, we want to develop a new kind of localized supply chain that is specifically tailored to retail experiences, which is more curated, community-driven and socially intimate.”
Some of these startups rely on volunteers and are modeled more like nonprofit organizations that rely on grants and donations. Others are attempting to create value for both farmers and consumers by charging either the farmer or the consumer for their logistics services. These startups are responding to increasing consumer demand for local food from small producers. But it’s not clear if this local supply chain can find a way to make money without working with the larger food distributors.
In Kenya, where large food distributors aren’t as common in the food system, Taimba seeks to tame a chaotic and fragmented supply chain by connecting farmers with retailers and vendors through a cashless business-to-business app. Vendors order their produce via the app, then Taimba retrieves it from the farmers and delivers it to the marketplace. Farmers receive a fair price for their goods, and vendors receive inventory at below-market prices.
“The ability to offer a market and good prices to small-scale farmers has really boosted farmers’ earnings by reducing wastage and paying promptly,” says founder Dominique Kavuisya. Taimba went home with one of three $10,000 Prizes.
While consumers everywhere want more local food, the system to deliver the goods is still awkward, unsustainable and encumbered by capital equipment expenses and the lack of technology and tracking on the small-producer side. We are anxious to see how our finalists work on solving these issues.
Through the innovative work of our contestant startups, we are optimistic that we will see more locally produced fresh produce reach consumers, less food waste in the landfill and better and safer products in our food system.
Prize winner Andreas Neuman of UAV-IQ with Food+City’s Robyn Metcalfe.
UAV-IQ’s monitoring technology in use.
Transaera founder Sorin Grama makes his pitch at the 2018 Challenge Prize.
Transaera’s technology absorbs moisture in greenhouses.
Map by Stowga representing available storage space in the United Kingdom.
Vinder founder and CEO Sam Lillie.
F+C’s Robyn Metcalfe with Prize winner Jonathan Partlow of Aggressively Organic.
Aggressively Organic’s hydroponic growing system with leafy greens.
Grit Grocery truck in Houston.
Grit Grocery founder Dustin Windham, right, visits with a supplier in the field.
F+C’s Robyn Metcalfe congratulates Dominique Kavuisya, Taimba founder and Prize winner.
FOOD+CITY Challenge Prize
Innovation in food takes all forms, from making improvements to pallets to creating new avenues for delivering food or designing packaging that increases shelf life. Since 2015, we’ve hosted a challenge prize for startups in the food space that are challenging our notions of how the supply chain works. The 2018 Challenge Prize was awarded on March 13, 2018, at SXSW Interactive. Visit foodandcity.org/prize to learn more about this year’s entrants and winners.