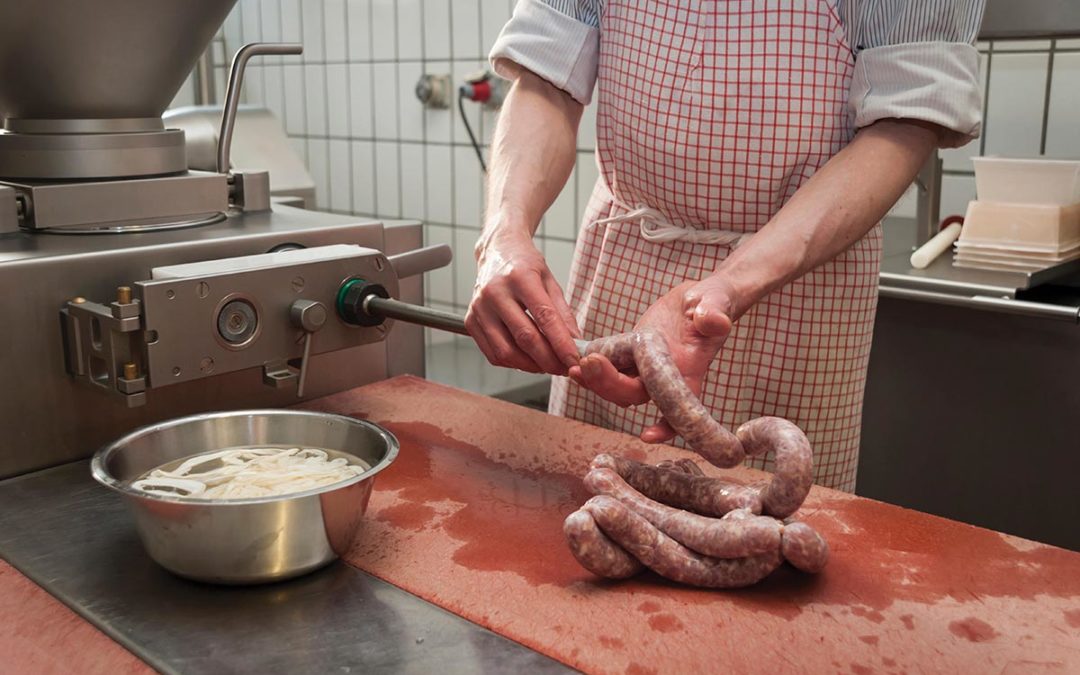
Protecting Provisions
Food packaging has been around as long as people have traded goods in markets. How else are you going to schlep that wine home across the desert? Given all that’s new in packaging and shelf-life technology, we’re taking a look back to some golden oldies, from skins and amphorae to the humble milk bottle.
Skins
Plants, animals and even humans have skins that inhibit the loss of water, so we will last longer. Food packaging performs the same function, inhibiting water loss and gain to extend freshness during transportation and storage. Too much water for any living creature causes cell death, so food scientists have been working for centuries to find the best way to provide a barrier between food and the environment.
Before the 17th century, that optimal barrier was literal skin. Leather bladders and other animal hides were convenient packaging materials beginning in prehistoric periods, and most “packages” for food were not removed during the cooking process. Animal bladders held meats and mixtures of vegetables and seasonings over the cooking fire. In a sense, haggis and natural sausage casings are modern-day versions of this ancient packaging.
Though we now have more options than our 17th-century ancestors did, we still protect many foods from spoilage by applying a protective skin.
Think of spoilage this way: Any perishable food ingredient, processed or unprocessed, breathes just like we do, taking in oxygen and releasing carbon dioxide. Bacteria grows faster if it exists in conditions that enable it to breathe, allowing it to break down the plant or animal cells. That’s why you frequently see cheeses and fruits covered with wax. The Chinese popularized this tactic during the 12th century, when they wrapped citrus fruits in wax to decrease the interior oxygen content and ensure the fruits made it to the emperor’s table. Different types of waxes (e.g., sugar cane and carnauba) are often applied by spraying or dipping fruits and vegetables to preserve or improve the appearance and protect the produce during storage.
Wax isn’t the only kind of protective skin: Victorians used lard to coat food, and M&Ms are covered with confectioner’s shellac, a substance made of an insect-derived coating that’s produced in India and called lac dye. Your french fries remain white and crispy because of a coating applied during processing to inhibit discoloration. Some other coatings aren’t so natural, including calcium acetate and calcium ascorbate. Even wheat gluten becomes a skin for some foods that are not grain-related at all.
Jars and Pottery
Three thousand clay jars of fermented fish sauce emerged gently from the sea in 2015. A team of archeologists led by Simon Luca Trigona celebrated their trove after two years of painstaking work around a Roman ship that was built sometime in the first or second century. These containters, called amphorae (singularly, amphora), have been around since the Neolithic Period (10,000 to 2,000 BCE). They were made of clay and often carried wine, oil or a fish sauce known as garum. The fish sauce, which resembled ketchup, was most likely from Spain and bound for Roman markets.
Fish sauce traveled in pottery vessels long before the sinking of the Roman ship. At the time, clay was also used as a sealant for baskets that carried grain. To eliminate the absorption of liquids by the vessel, clay, resin or pitch coated the interior surfaces. Manufacturers of amphorae applied a stamp to the outside that indicated its origin. In some cases, other information would be written or painted on to indicate weights, contents and market information.
Not often recycled, Greek and Roman amphorae were broken up after they reached their destinations. Rome’s Monte Testaccio is a mountain of these vessels, a Roman pottery garbage heap.
Glass, Crates and Cartons
Milk travels along the supply chain in bulk and consumer packaging, contained in glass, plastic and paper. A rusty milk jug worked its way up to the soil surface in our backyard last summer, with a metal label indicating it had belonged to the Turner Center Creamery in Auburn, Maine. The creamery, which operated in Auburn in 1893, manufactured the first commercial ice cream in New England. Customers would send jugs to dairies where the farmers would refill and deliver the milk back to the customer.
In more urban areas, metal milk jugs had been replaced with glass bottles topped with metal caps. Alexander Campbell introduced these bottles in 1878 in Brooklyn, New York, and by the early 1900s, fiber material and paraffin covered the metal caps. At first, customers resisted the glass bottles because glass was commonly used for medicines from the drug stores, and dairies worried about broken glass. But distributors preferred glass for sanitation and easy handling, so both dairies and consumers overcame their concerns, and glass replaced the metal jugs until paperboard appeared in the early 20th century.
In 1915, John Van Wormer patented a wax-sealed paper carton with a gable top that could be shipped flat for assembly at the dairy. Gallon and half-gallon plastic jugs became the preferred package for milk by 1970, but paper milk cartons have made a comeback since being fitted with screw tops in the 1990s.
Plastic jugs travel to stores in milk crates, which were once made of metal, but were replaced with plastic by the 1960s. Each crate carries four to six one-gallon plastic milk jugs. About 20 million crates go missing every year, stolen for shredding and reselling at a profit. The International Dairy Foods Association (IDFA) estimates that U.S. dairy companies spend between $80 and $100 million to replace stolen or missing plastic milk crates (read about another beverage container that often falls out of the supply chain).