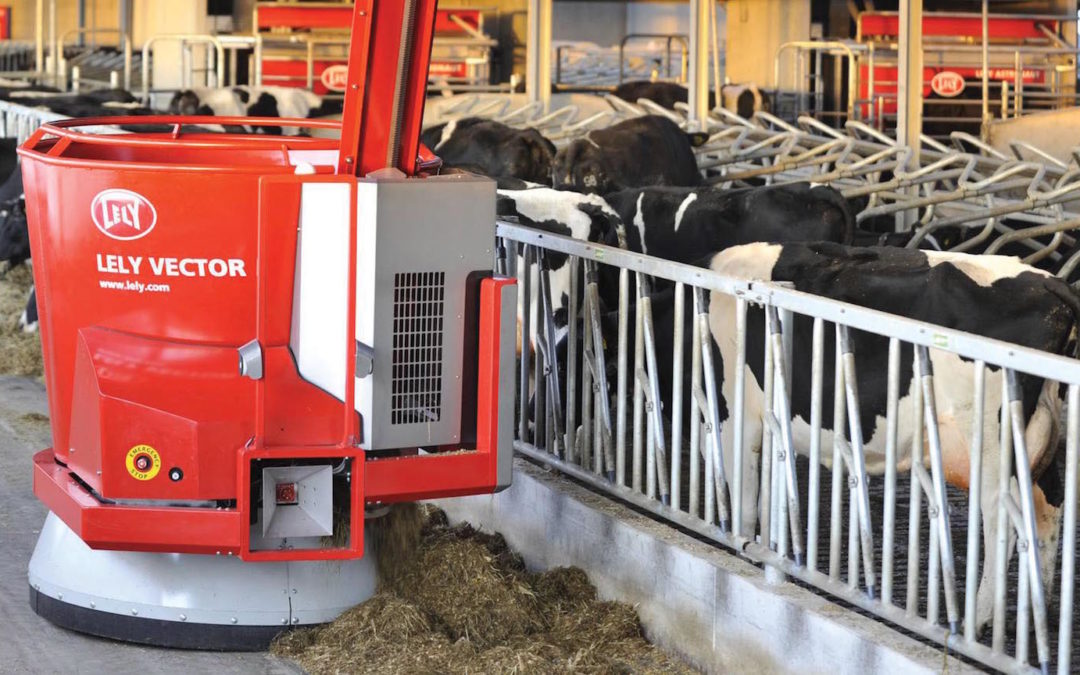
Food Movers: Robots as Farmhands
Every day there’s a new story about robot bartenders on Carnival Cruise Lines or Domino’s Pizza delivery pods trolling the streets in Europe. For now these are mainly stunt-bots, more public relations than practical. Yet there are already many kinds of robots at work in our existing food supply, albeit models slightly more mundane.
Whether robots (and their engineers) will totally replace regular workers is still up for grabs, but in truth bots will soon be everywhere in the supply chain: Packing and warehousing, farming, food processing and, yes, even hamburger flipping and order taking.
This is the first in a series on food bots, starting with a deeper dive into three cases where bots have taken over some of the dreariest jobs in mass production — repetitive, physically stressful, low-paying, dead-end, sometimes dangerous — that many humans would rather not do.
BOT
a device or piece of software that can execute commands or perform routine tasks either automatically or with minimal human intervention.
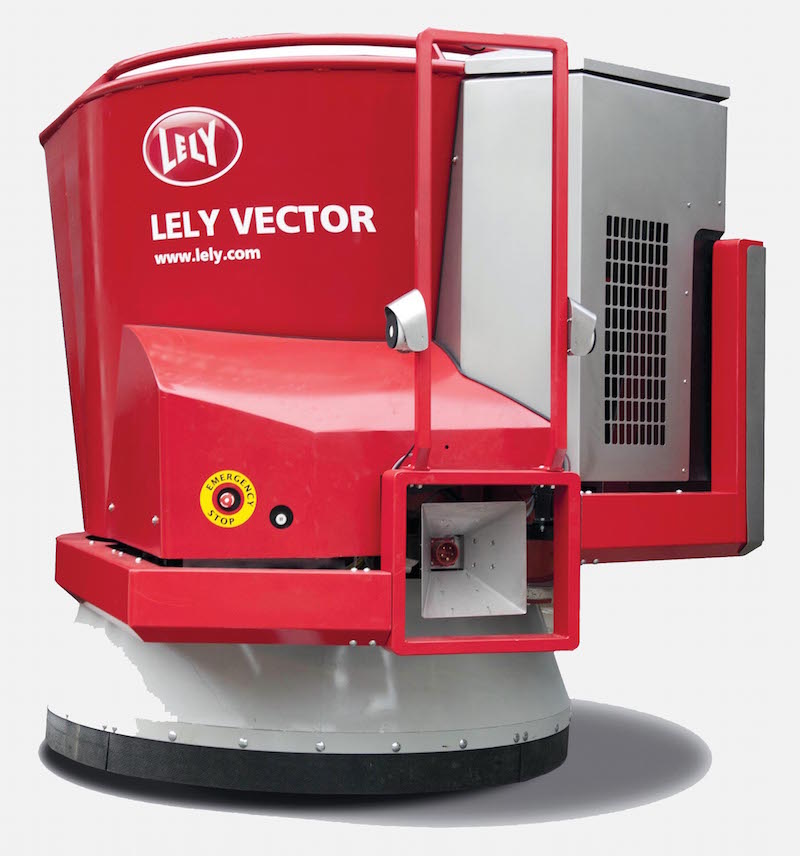
THE FEED BOT
A Dutch dairy technology company called Lely makes Vector, a battery-powered feed bot that looks like a slow-moving escapee from the teacup ride at a state fair. Its speed belies its benefit to a working dairy barn: Consider that a cow can eat for six hours per day, and dairies feed hundreds of cows. Vector uses lasers, ultrasound sensors and metal guides to keep on track as it slowly scoots around, distributing feed, and then plugs into a docking station to recharge during downtime. Vector re-ups with silage — aka the mix of grasses, corn, sorghum and other grains dairy cows need for good-tasting milk — using a laser-assisted claw that serves up the proper proportions. (Watch the Vector do its job.)
Inside the robot’s 600-kilogram basin is a mixer arm, which automatically starts to blend different types of food together as soon as they hit the bowl. The system can prepare different formulas based on which groups of cows Vector needs to feed.
The constant spinning of the robot’s “skirt” brushes feed up along the open gates of a cattle barn, where the cows can easily get to it. The robot glides around until its laser finds a spot low or empty of feed; a sliding door rises up and feed settles out.
THE PICK AND PLACE BOT
One of the more common robotic technologies used in the food industry is “pick and place,” which is exactly what it sounds like. These robots move things from one place to another with lightning-fast speed. They’re also making basic decisions, thanks to digital cameras and other tools that let the robots “see.” As things come down a conveyor belt, for example, robots rotate and place items into the proper packages, or — with the addition of special tools — score bread loaves, decorate cakes and swish sauce across pizzas (watch it sauce pizza). Many work something like ABB Robotics’ IRB 360 FlexPicker, which hangs from above and look like a giant daddy longlegs. Skinny metal arms triangulate to pack cookies, beers, cherry tomatoes, beef jerky, pancakes or — with some heavy-duty models — even boxes or pallets.
The bot “sees” using mounted cameras connected through network software, which means it can find objects when they’re overlapping and in random positions. The “hands” can be suction pads, “fingers” or special tools for slicing or spreading.
Pick-and-place robots handle more than 15 pounds and can relocate things up to five feet, making their moves in less than a second.
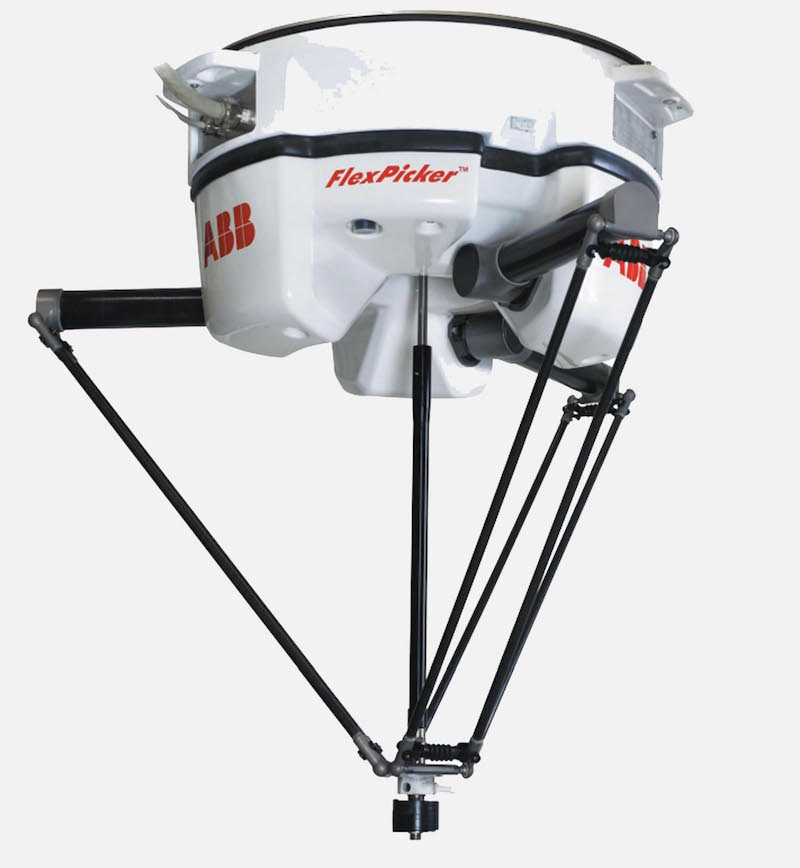
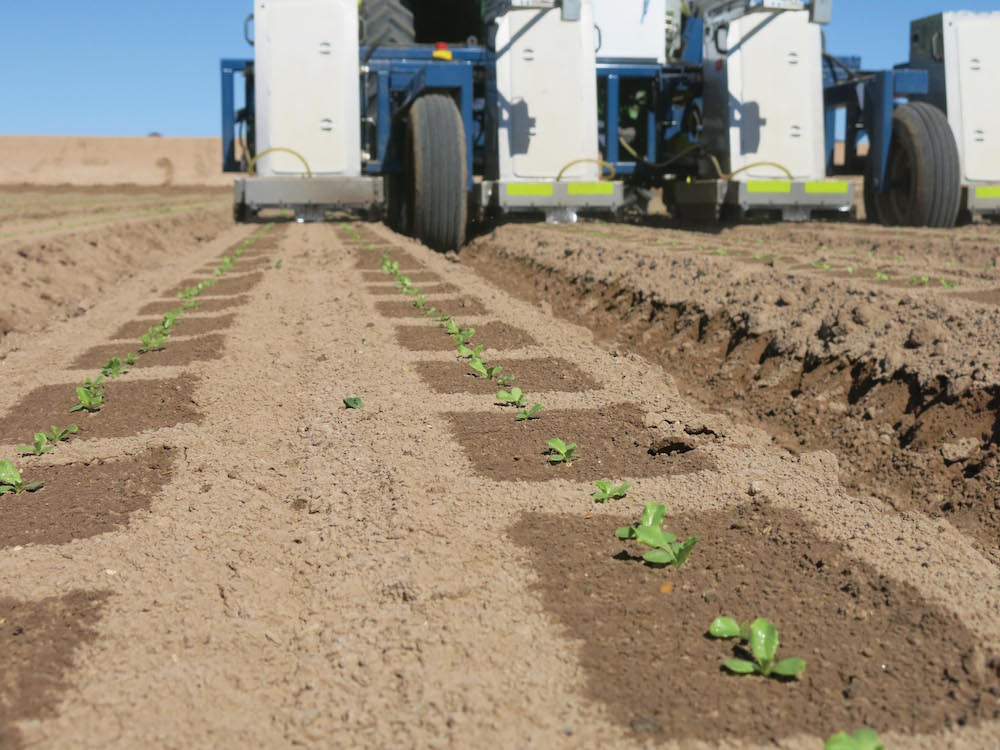
THE SEE AND THEN DO BOT
More advanced robots work by combining the sensor technology used above — cameras, 3-D mapping and digital “vision” — to execute more complex actions. A handful of companies make robot systems that can process meat, for example, using 3-D scanners or X-rays to map the bone placement of pork sides or lamb carcasses. The robot arms — its fingers would be the knives — react within seconds to make the right cuts. More mobile versions of these systems are also applied to farming: In California, Blue River Technology’s LettuceBot uses computer vision to see fields as it crawls them, perfectly thinning lettuce starts in vast fields (watch it work). Other farmbots include Hortibot, which can see weeds and treat them, a RowBot made for dense cornfields and an Agrobot that travels down a raised bed of strawberries scanning each plant and harvesting only the ripe, red fruits.
The LettuceBot attaches to an ordinary tractor, then uses camera systems to see plants in 3-D as they roll by. It picks out which to thin and which to keep in less than a second. Blue River Technology uses the term “see and spray,” as in the bot sees the plants in a field and precisely sprays only the lettuce plants to be thinned. The LettuceBot processes thousands of plants per minute with an accuracy of a quarter of an inch, says the company. Most people rent them by the acre for the vast lettuce farms of California and Arizona.